Since March 2020 the distributed workforce has become normal for most industries with a high...
Here comes the paper: optimising scanner throughput
Continuing on from last month where we discussed the benefit of VRS in document processing, this month we touch on the ‘engine’ of the physical capture process – scanners.
Whilst VRS is an extremely powerful tool, the benefits of the image processing software can be scuppered with a poor start, VRS will deal with a lot but optimisation looks at all aspects of a process holistically not in isolation.
To give you a brief analogy, why put super-unleaded (99) fuel in a Golf V6 for ultimate performance if you don’t follow the rest of the maintenance schedule on the vehicle (oil, sparks, filters etc)? Yes you might get a slightly cleaner combustion chamber but you will not gain any performance from that extra outlay – a waste of effort.
There is an expectation that whatever agreement emerges with the EU, there is going to be more paperwork, more complex processes and therefore a need to streamline as much as possible to minimise the time / cost to a business. (Again, see last month’s VRS article) Couple this with a slow return of employees to an office scanner that has potentially not been used in a while and a backlog of documents, you could have a process bottleneck on your hands.
As a general rule, these are the precautions / preparations your business should take in preparing to use your document scanner:
Clean your scanner path:
Check the scanner for rogue paper clips or discarded staples. Use a vacuum with a soft brush attachment to gentle lift paper dust out of the trays / image path. Wipe over surfaces with a soft, lint free cloth dampened with water if required.
Clean the imaging guides and roller tyres – below are a couple of examples for the popular Kodak i3000 series scanners which shows the principle that can be applied across many models / manufacturers. They recommend the use of ‘staticide wipes’ but a damp (water only) clean, lint free, soft cloth will do.
Check for wear:
If the tyres on the roller assembly have gone shiny / flat (little ribs have worn flat), then a replacement set is required. Talk to support who can advise on a price and arrange delivery of the parts.
Check for damage:
Having cleaned the imaging guides, look for scratches in the lens surface. These defects can lead to poor performance with skew, automated page size detection and especially image quality with line ‘artefacts’ through images. If there is any damage visible, talk to support who can advise on a price and arrange delivery of the parts for replacement.
Squeaks and/or rattles:
Talk to our support team who can arrange an engineer visit to fully service and diagnose any further issues. If the scanner is under a maintenance contract, only replacement parts would be chargeable (excluding warranty items), otherwise PacSol can arrange for a chargeable (T&M) engineer visit.
Total failure:
You have tried everything and following an engineer visit the device is either considered ‘dead’ or beyond economical repair. Fear not, talk to us at PacSol and we can offer competitive pricing on a whole range of scanners, most of which can be delivered within a day or two. Once the scanner has arrived onsite, our support team can assist with the initial setup / driver changes to have you up and running once again.
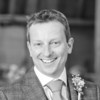
Toby Gilbertson, Customer Services Manager. November 2020
#pacsoluk #kofaxvrs #documentcapture #documentmanagement